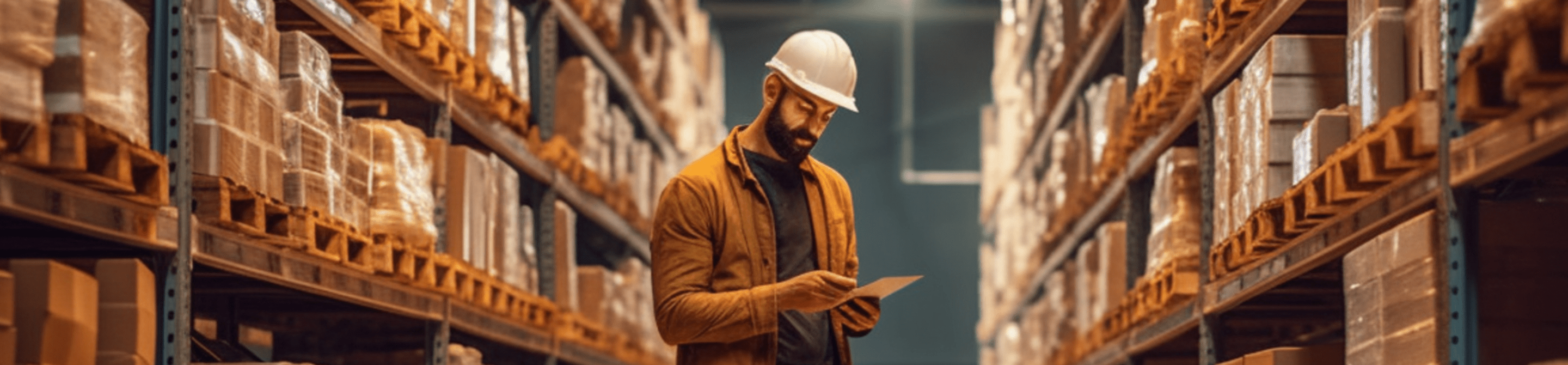
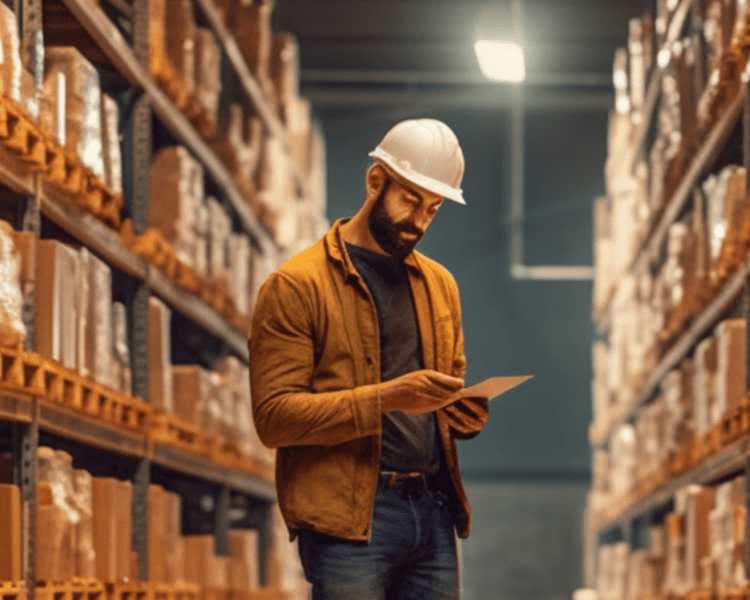
Occupational Health and Safety
Highlight Performance 2024
Safety Fatalities
Illness
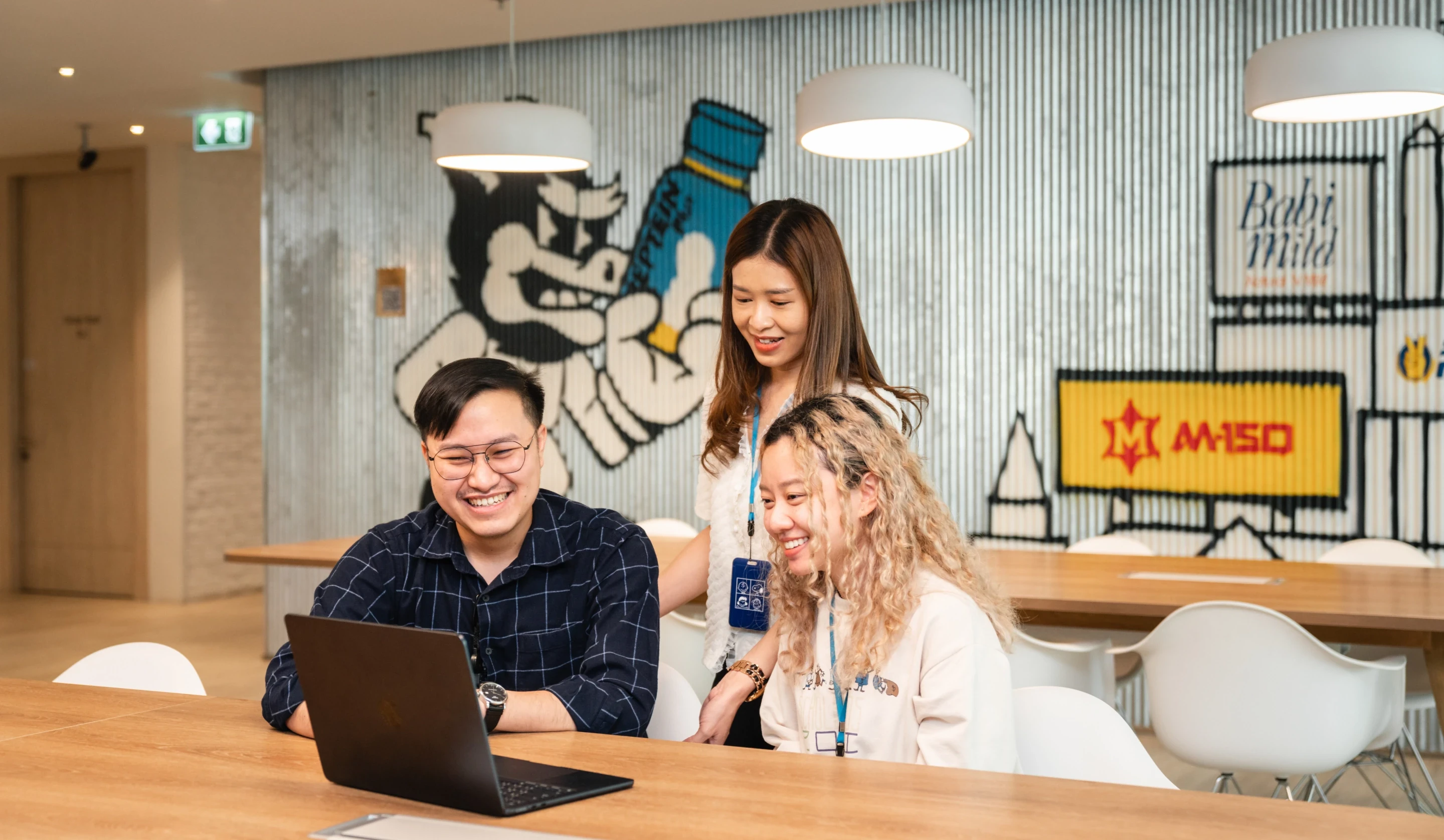
Treating Employees according to Sound Labor Practices and Promoting Human Capital Development
Osotspa has developed a holistic human resource management strategy that aligns with the core value statement of the Company: “the power to enhance life for consumers and community through a culture of high performance, innovation and sustainability”. This strategy achieves the Company's goal of increasing employee motivation, fostering engagement, retaining talented individuals prepared to enrich and advance the organization, supporting employee development, promoting a safe workplace environment, and cultivating mutual respect among all individuals. All of Osotspa’s employees play an important role in promoting and driving the organization's sustainability.
Fostering a Healthy and Safe Work Environment
Our top priority is to provide a safe and healthy work environment for our employees. To help prevent workplace accidents and illnesses, promote employee welfare, and ensure that the work environment stays in line with local laws and safety standards as well as international regulations, the Company has employed the "SHE Vision Zero" campaign. We are committed to being a sustainably safe organization, free of workplace accidents and occupational illness, where employees are healthy and environmentally conscious.
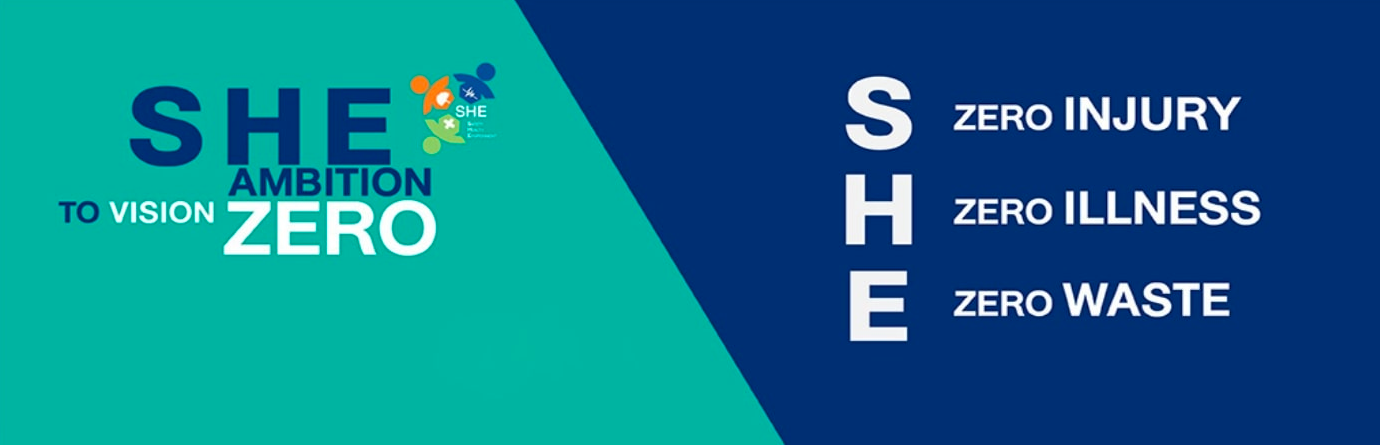
Occupational Health and Safety Operations
Osotspa fosters a culture of safety and continuously improves its safety management system to stay in line with international standards.
Hence, the Company has established the Occupational Safety, Health and Working Environment Committee (OSHEC), which collaborates with all sectors within the organization. This committee is responsible for setting operational guidelines and closely monitoring occupational health and safety performance to ensure that employees, contractors, and suppliers work efficiently and in compliance with established standards. Additionally, the Company has implemented international safety performance indicators to monitor and assess safety operations, such as the Injury Rate (IR) and the Lost Time Injury Frequency Rate (LTIFR).
Injury Rate - IR
(cases per million working hours)
2020 | 2021 | 2022 | 2023 | 2024 | |
---|---|---|---|---|---|
Employees | 1.98 | 3.61 | 2.48 | 2.08 | 2.05 |
Contractors | 0.67 | 2.20 | 1.39 | 0.59 | 0.20 |
Lost Time Injury Frequency Rate - LTIFR (cases per million working hours)
2020 | 2021 | 2022 | 2023 | 2024 | |
---|---|---|---|---|---|
Employees | 0.54 | 0.45 | 0.35 | 0.49 | 0.15 |
Contractors | 0.67 | 0.79 | 0.62 | 0 | 0 |
Fatalities
2020 | 2021 | 2022 | 2023 | 2024 | |
---|---|---|---|---|---|
Employees | 0 | 0 | 0 | 0 | 0 |
Contractors | 0 | 0 | 0 | 0 | 0 |
Reflecting our commitment to occupational health and safety management, the Company added various safety projects in 2023. These projects, alongside effective occupational health and safety management, resulted in the Company successfully reducing the Total Recordable Injury Rate and the Lost Time Injury Frequency Rate of both employees and contractors.
Related Standards & Certificates
Plant Location | Safety-related Standards & Certifications | |||
---|---|---|---|---|
Thailand Safety Excellence Award (Department of Labor Protection and Welfare) | Thailand Vision Zero Award (Safety and Health at Work Promotion Association) | Zero Accident Campaign (Institute for Occupational Safety, Health and Environment) | ISO 45001: 2018 | |
Beverage Filling Plants | ||||
Beverage Filling Plant, Huamak, Bangkok | ||||
Beverage Filling Plant, Ayutthaya | ✓ | ✓ | ||
Beverage Filling Plant, Min Buri, Bangkok | ||||
Personal Care Plants | ||||
Liquid Personal Care Plant, Greensville Factory, Ladkrabang, Bangkok | ✓ | ✓ | ✓ | ✓ |
Powder Personal Care Plant, Greensville Factory, Ladkrabang, Bangkok | ✓ | ✓ | ✓ | ✓ |
Glass Factories | ||||
Siam Glass Industry Factory (SGI), Samut Prakan | ✓ | |||
Siam Glass Ayutthaya Factory (SGA), Rojana Industrial Park, Ayutthaya | ✓ | ✓ | ✓ | |
Siam Glass Industry Factory (SGI-AY), Ayutthaya | ✓ | ✓ | ✓ | ✓ |
Cullet Treatment Plant (SCL), Saraburi | ✓ | ✓ | ||
Other Facilities | ||||
Label Printing Factory, Chatuchak, Bangkok | ||||
Osotspa Beverage Factory (Siam Beverage) | ✓ | |||
Warehouse, Ladkrabang, Bangkok | ✓ |
Performance Highlights
Osotspa controls occupational health and safety risks in the workplace by implementing effective safety tools, including the “Near Miss Reporting, Safety Suggestions, and Safety Patrol” scheme. We follow a set of procedures that help track potential incidents in order to improve operations and enhance safety. Reported close-calls or near accidents are investigated to determine the causes and the appropriate actions needed to prevent recurrence or other future accidents.

In the event of an accident
The company immediately implements proper corrective actions and launches an investigation to determine the cause. Such information must be recognized by the manager of the site where the accident occurs. Every accident must be reported to senior management as soon as possible
Lesson Learned Card (LLC): The tool allows companies in Osotspa group to share information about accidents and safety improvements. It equips operators with the knowledge they need to avoid future incidents.
Safety System Software: To improve operational efficiency and reduce accidents, the company encourages employees report unsafe incidents through online systems such as the Safety Patrol for reporting unsafe accidents, the Near Miss Reporting, the Safety Suggestions for receiving suggestions, and the Kaizen system.
These online systems allow operators and relevant persons to track progress in resolving issues and increases monitoring and improvement efficiency
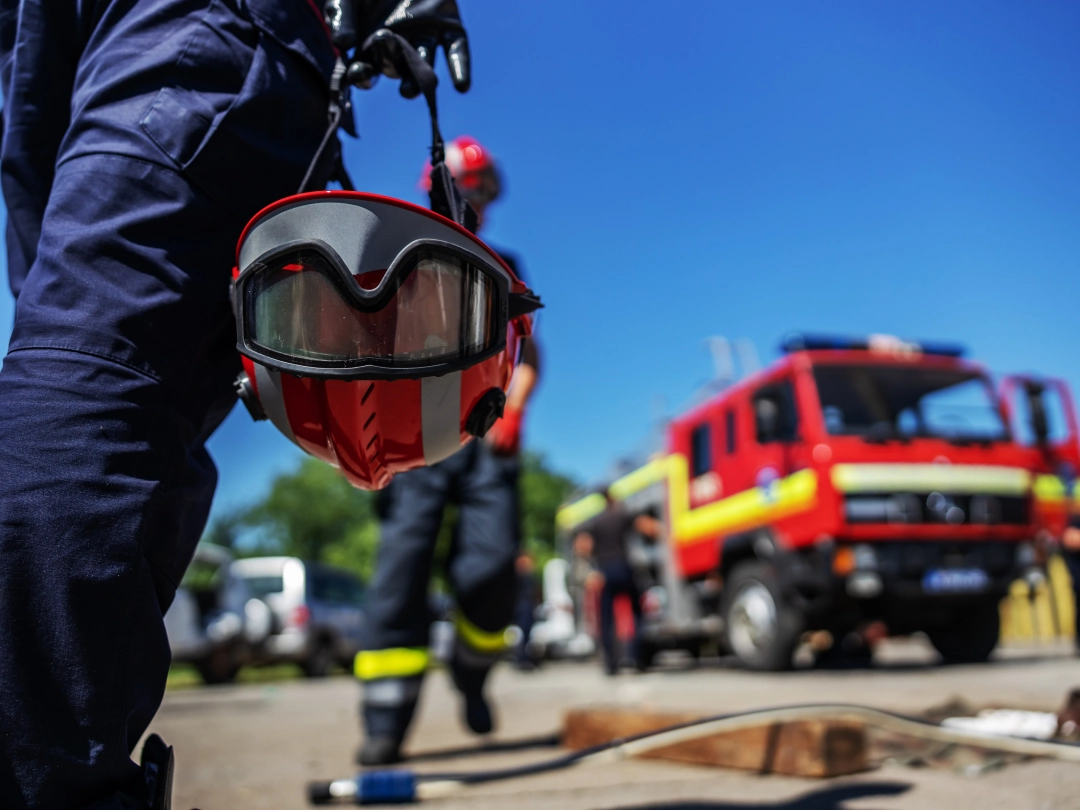
Emergency Response Readiness
Every function in the Company must regularly review and improve its emergency plans, which include their response to fire incidents, chemical spills, floods, critical contagious disease outbreaks, etc. In addition, in each organization, the responsible persons and their roles in the event of an emergency must be defined and updated. Incident response drills must be conducted as planned in order to effectively prepare for and reduce the risks that may arise in the event of an emergency.
Emergency equipment, including fire extinguishers, chemical recovery equipment, flood protection equipment, etc., must be checked and maintained to ensure availability.
Every function in the Company must regularly review and improve their emergency plans, which include their response to fire incidents, chemical spills, floods, critical contagious disease outbreaks, etc. In addition, in each organization, the responsible persons and their roles in the event of an emergency must be defined and updated. Incident response drills must be conducted as planned in order to effectively prepare for and reduce the risks that may arise in the event of an emergency.
Emergency equipment, including fire extinguishers, chemical recovery equipment, flood protection equipment, etc., must be checked and maintained to ensure availability.
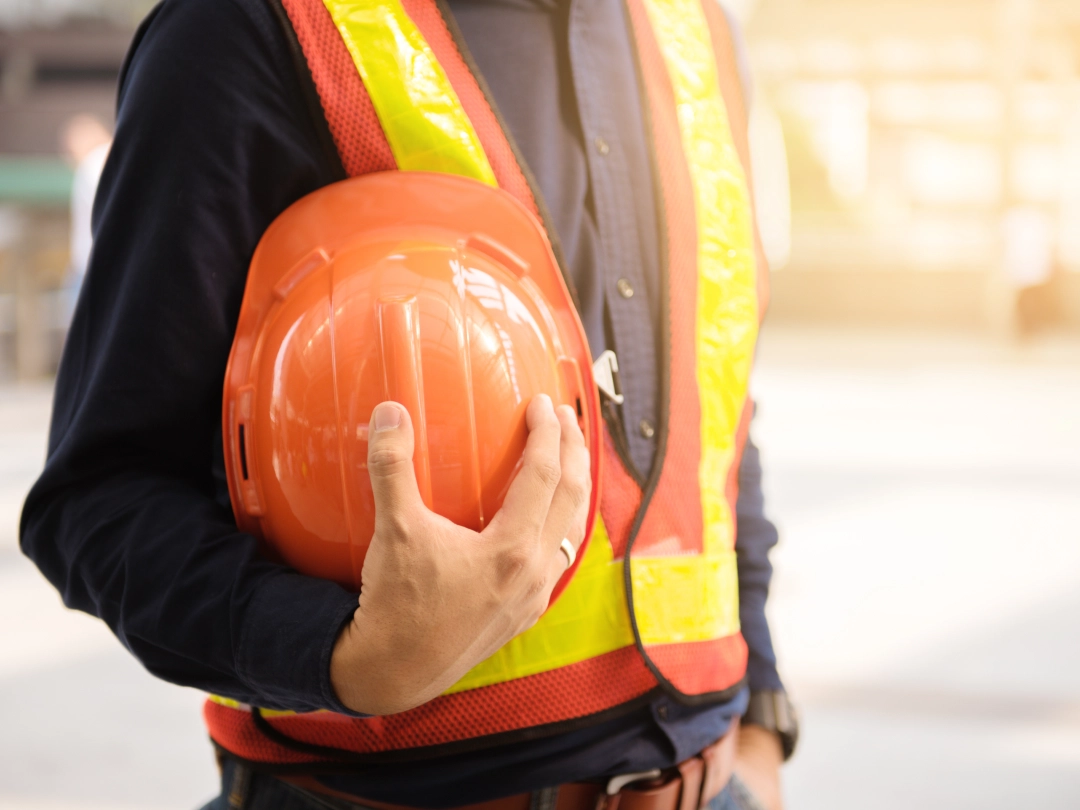
Behavior-Based Safety (BBS)
We believe that a positive safety culture 1) encourages individuals within a workplace to take responsibility for their own safety and the safety of those around them, 2) enhances the Company’s overall safety culture, and 3) expands activities associated with workplace safety.
The company has thus implemented the principles of Behavior Based Safety (BBS) with the goal of reducing the number of workplace accidents by changing employee and contractor safety behavior.
In 2024, BBS programs were implemented at seven of Osotspa's operational sites. The company plans to institute BBS in all departments to instill a safety culture throughout the entire Group.
Building a Culture of Safety
Reporting of Near-Misses and Safety Inspections
Osotspa encourages employees, contractors, and all personnel working on-site to report near-misses and unsafe conditions through the Near Miss Report software and Safety Patrol software, both of which are electronic systems. The Company collects and analyzes these incidents to identify causes and appropriate corrective actions. Additionally, Osotspa plans and implements improvements to reduce the likelihood of accidents and prevent recurrence.
Near - Miss Reporting Software Reporting of Near-Misses
Safety Patrol Software Reporting of Unsafe Conditions
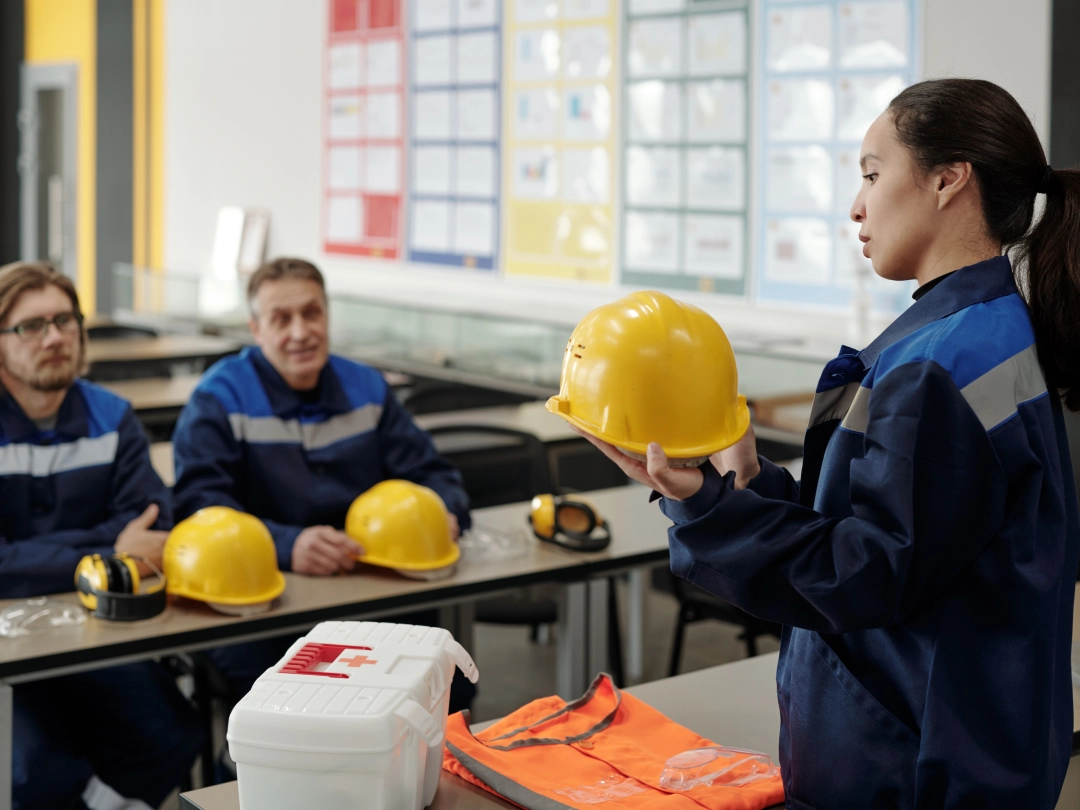
Safety Training
Osotspa provides ongoing safety training through both online and onsite channels for employees to enhance awareness and promote a culture of safety in the workplace.
The Company has introduced new training regimens under the names “SHE e-Learning” and “SHE MS Software,”
aiming to ensure that employees understand occupational health and safety principles and can perform their daily tasks safely.
Total Training Hours: Employees
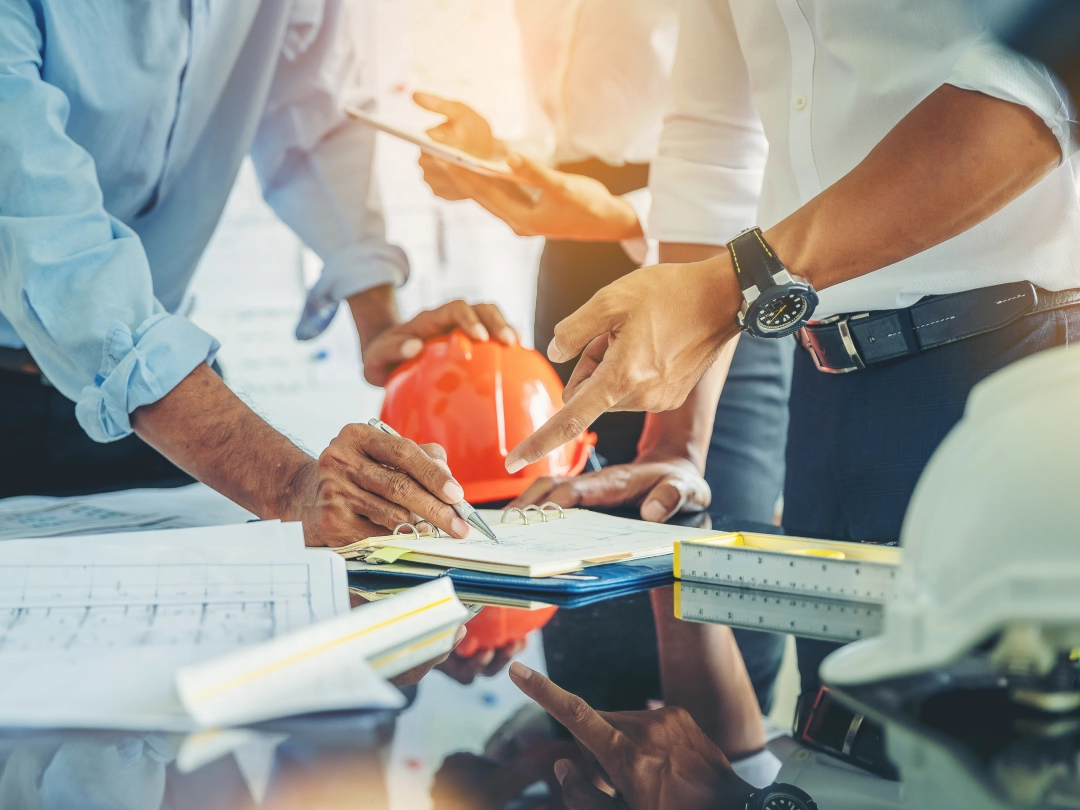
Mandatory Course for All Employees
- Safety training for new employees before starting work: 6 hours
Mandatory Course for Relevant Personnel
- Safety Personnel
- Safety Officer Supervisor Level
- Safety Officer Management Level
- Safety Committee
- Use of SHE MS Software
- Safety and Environmental Standards – Osotspa Group
- Basic Firefighting and Fire Evacuation Training
- Basic First Aid
- Crane and Hoist Operation Supervisor Training
- Safe Driving for Vehicles, Forklifts, and Loaders
- Chemical Management and Emergency Response for Chemical Spills
- Behavioral Safety Improvement
Training Course for Contractors
The Company requires all contractors working on-site to undergo safety training, including relevant safety standards, before starting work.
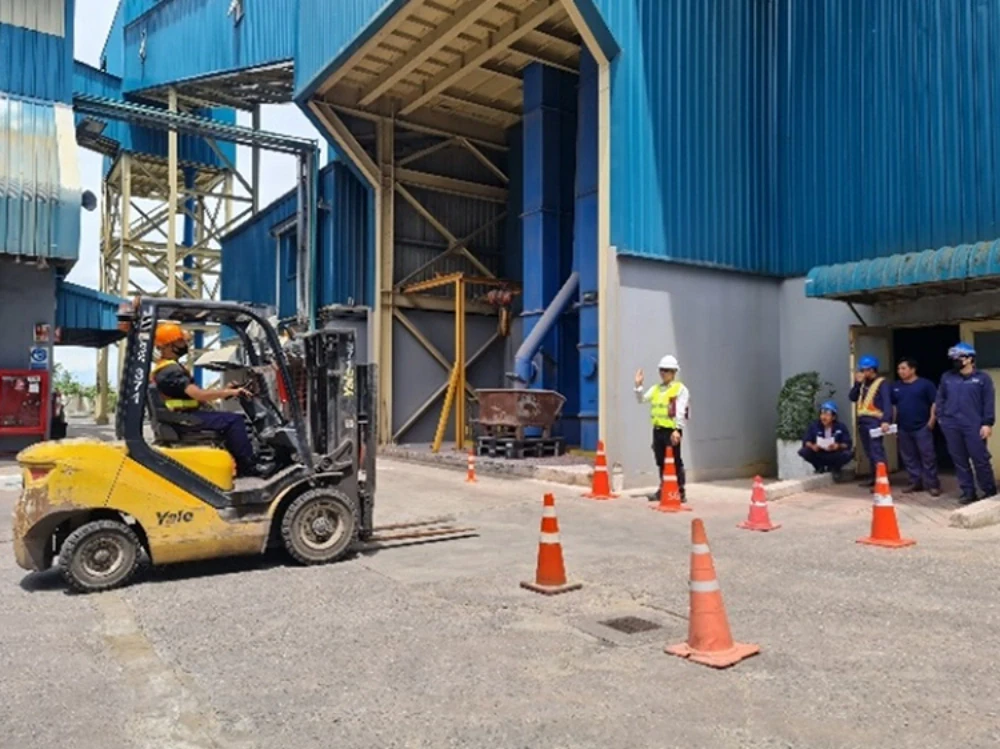
1. Safety, Occupational Health, and Environmental Regulations
- Osotspa Safety Policy
- General Workplace Safety Personnel must wear appropriate attire, including long-sleeved shirts and long pants without rips, safety shoes, and personal protective equipment (PPE) as required by the job. Contractors must also wear ID badges and training certification passes. Driving speed must not exceed 20 km/h, engines must be turned off when parked, and smoking is only allowed in designated smoking areas.
- Waste and waste management Disposal of waste, liquids, or chemicals of any kind onto the ground, into drainage channels, or into pipelines is strictly prohibited. Contractors must provide appropriate containers for chemical storage. Machinery and tools that use oil or lubricants must always have a drip tray in place during use or maintenance.
- Basic Fire Prevention and Suppression In case of an emergency, such as a fire, employees must follow the emergency response plan (objects must not be placed in the way of fire extinguishers/fire extinguisher cabinets, fire alarms, and employees must learn how to use fire extinguishing equipment and escape routes) and proceed immediately to the designated assembly point for each area.
- Additional Prohibitions and Penalties Bringing illegal drugs, alcoholic beverages, or intoxicating substances into the Company is strictly prohibited; individuals under the influence of alcohol or drugs are not allowed to enter or work within company premises. Children are not allowed within the Company’s premises. Violations will result in disciplinary action in accordance with the company’s policies.
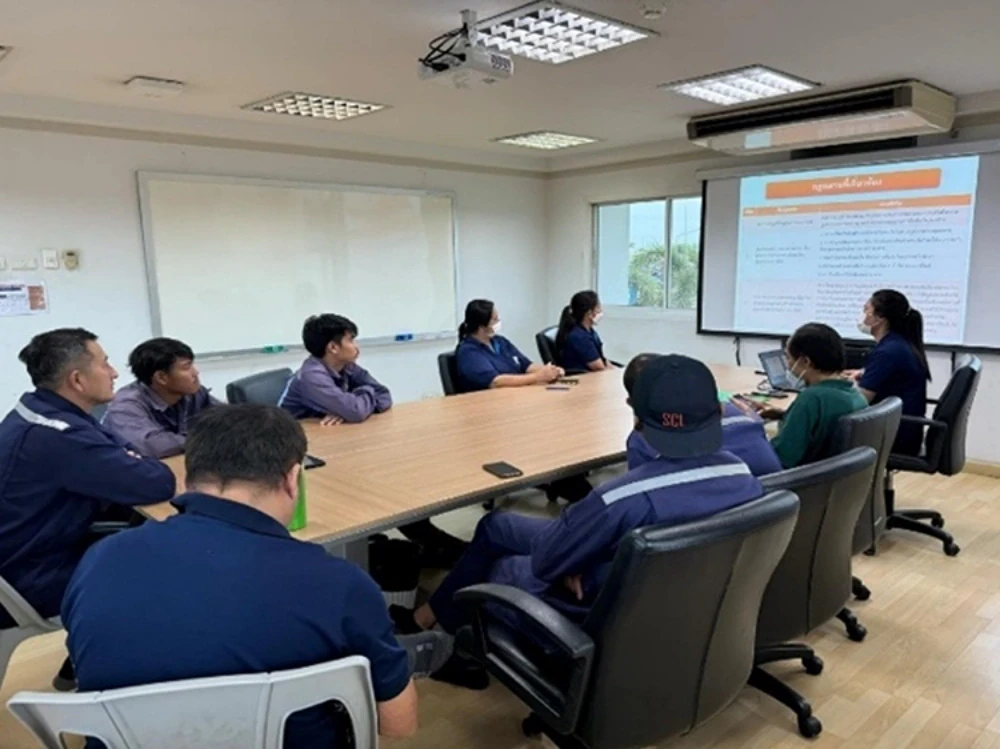
2. Guidelines for Ensuring Safety and Occupational Health and Environmental Standards
- Personal Protective Equipment (PPE).
- Construction, renovation, or modifications inside buildings require written permission to access the area.
- High-risk work, including confined spaces, working at heights, spark-generating tasks, and excavation, requires daily work permits.
- Safety in excavation work.
- Safety in working at heights when there is risk of falling from elevated or sloped areas.
- Scaffolding and shoring work, and safety in scaffolding usage.
- Confined space work.
- Spark-generating tasks.
- Crane operation.
- Forklift operation.
Measures to Ensure Employee Health and Safety During Epidemics/Pandemics
The Company closely monitors the spread of various diseases to ensure that all relevant departments can effectively and swiftly implement control measures in case of an outbreak. The Company has reviewed epidemic control plans, including simulation drills for handling monkeypox outbreaks. Additionally, scenario-based training sessions are conducted in meeting rooms to prepare for emergency situations, such as future disease outbreaks.
Risk Assessment of Hygiene and Safety in the Work Environment During Operational Procedures
Osotspa requires all factories to conduct an annual review of occupational health and safety risk assessments to ensure that all existing work activities as well as new activities are properly assessed for risks and have appropriate control measures in place. This process is carried out in compliance with ISO 45001 standards.
Measures to Prevent and Reduce Hygiene and Safety Risks in the Work Environment During Operations
One of the Company's occupational health risks is the risk of Office Syndrome. This in mind, the Company has developed promotional materials to support employee health and organizes morning exercises and stretching activities before starting work each day to reduce the risk of work-related illnesses.
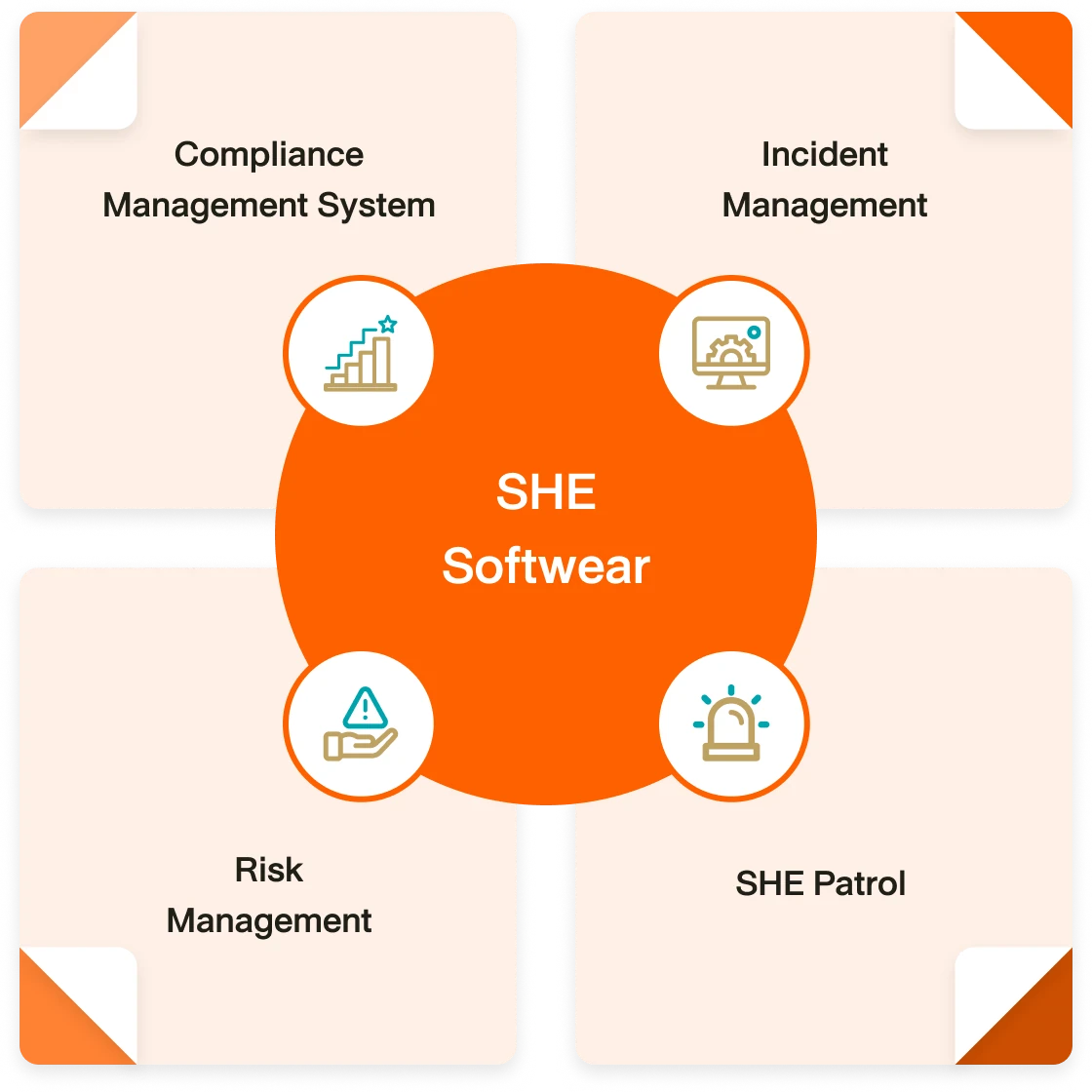
Safety Software
SHE-specialized management software was adopted for data connections across operations. The software facilitates synergies between the SHE function and other supportive operational units.
In addition, SHE software helps the company ensure company-wide compliance with applicable regulations and requirements while saving time and effort in the process.
The company improved the statistical data of the software system for easy inspection and efficient data usage through the Incident Management system and expanded the scope of use to our overseas operations. We prioritize auditing of legal compliance, revisions, and monitoring using the SHE software system, which covers all laws applicable to the Company. We also encourage operators to keep a record of safety inspections and improvements in the Safety Patrol system.
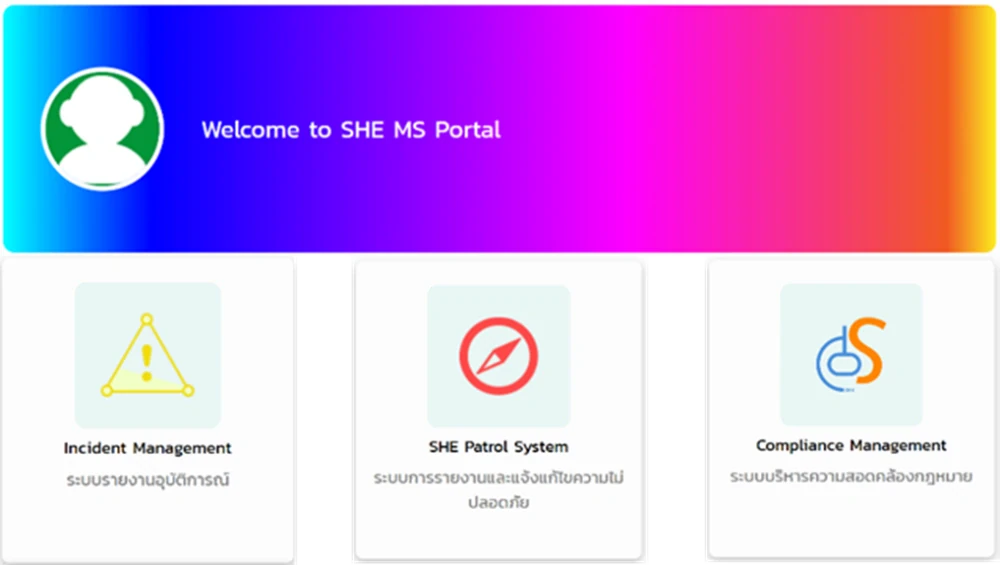
Example of SHE MS Portal
Using Safety Software to Enhance Work Efficiency
Osotspa has implemented Safety, Health, and Environment Management System Software (SHE MS Software) since 2019 to facilitate the integration of operational data across SHE functions and related departments within the organization. Each department can access and monitor data through the SHE MS Portal at any time, improving efficiency and allowing for seamless data retrieval for analysis. Additionally, the Company has made the following improvements to the SHE MS Software:
- Upgraded the Risk Assessment Module to align with ISO 45001 requirements by migrating the SHE MS Software server to AWS Cloud. This enhances user accessibility, reduces the risk of cyberattacks, and strengthens data leakage prevention.
- Improved the workflow of the Patrol Module to suit real-world cases and expanded its usage to the Quality Department of the personal care manufacturing group.
- Developed an automated legal review tracking function within the Compliance Management System (CMS) to ensure comprehensive monitoring and compliance with legal requirements.